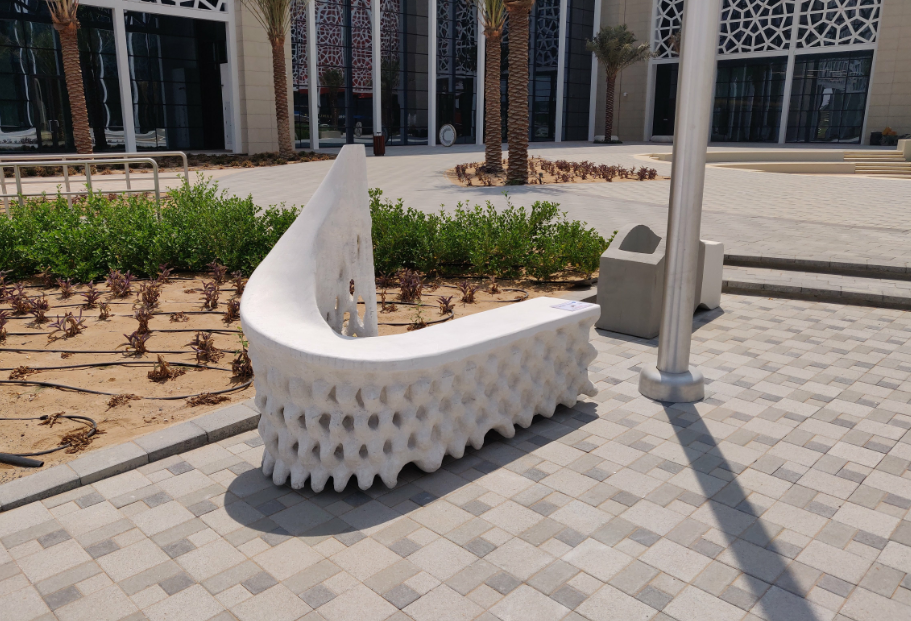
Advanced Construction Material
D-Shape: 3D Construction Printing Solutions (Powder Particles)
Vendor: D-Shape Limited
Origin: Europe
Tel: 9401 5270 (Mario Nuzzolese); Email: mario.nuzzolese@d-shape.com
The D-Shape offers a 3D printer that can create objects of any shape and size without the limitation of traditional manufacturing methods. It works by depositing a liquid binder onto a powder bed made of solid reactants and aggregates, which are then layered to form the desired object. This technology has many advantages over traditional manufacturing methods, including sustainability – it uses local materials such as crushed rock, sand or gravel; or recycled material such as shredded tire or leftover plant matter - allowing for unique textures and colours in each piece crafted.
Moreover, this 3D printing method is highly cost-effective since it requires fewer resources than conventional production processes while still producing high-quality products with intricate details. Additionally, its large-scale capabilities make it ideal for quickly creating complex structures on-site instead of transporting them from offsite factories – reducing both costs and environmental impact associated with transportation emissions. The process also eliminates waste created during production due to its precise layer-by-layer approach that only uses what's necessary for the job.
Finally, the D-Shape offers unlimited design possibilities thanks to its ability to craft pieces out of almost any material imaginable. From jewellery to furniture, art installations to architecture, there's no limit to building whatever your imagination desires! Not only does this offer designers incredible freedom, but it also allows them to create truly unique pieces unlike anything else available in today's market.
Before printing, a 3D model is sectioned into discrete layers using a computer program and determine where and how to spray the structural ink. When running, a printer ‘head’ of 300 nozzles at 20 mm intervals runs the entire length of the x-axis. Several passes interlaced together make a single printed layer. The printer has a rate of circa 20 cm per hour. Material costs are relatively low – solid, and liquid binders are cost-competitive. Aggregates are procured from fine powder wastes from local quarries. The physical characteristics of the printed material are comparable to a stone. According to recent research, the ultimate tensile strength of printed material is 25 MPa. Limestone and other engineered stones often fall within the same range of characteristics. Printed designs are often rough because of the liquid moving by capillary action.
The most evident advantage of the D-Shape over other methods of casting or CNC manufacturing is the sheer flexibility given to designers. Voids within the structure are created very precisely. No complex moulds need to be made so that a complex shape can be cast using a 3D model. Straight edges are unnecessary with the D-Shape because it is cheaper and more accessible – organic shapes of all sizes are possible.
Benefits :
- Complex geometries
- Print on demand
- High Productivity
- Low Carbon Footprint
Applications :
- Adaptive infrastructure
- Marine repopulation
- Coastal protection
Project Reference :
- Acciona Dubai 3D Printing Centre
- Monaco Larvotto Reserve
- Anholt Offshore Wind Farm in the Kattegat
- South Runway Artificial Reef Project HK Airport Authority